この記事では、トヨタ生産方式「7つのムダ」をもとにした、業務の効率化について紹介します。
「いつも仕事が忙しくて残業ばかり。もっと自分の時間が欲しい……」
「何でこんなに毎日忙しいんだろう……人手が足りないだけ?」
人手不足だとしても人件費がかかるので、簡単には会社も人を増やせません。
そうなると、残業を減らし自分の時間を作るには「仕事や業務の効率化」しか手がありませんよね。
そんな業務効率化に活用される考え方、トヨタ生産方式「7つのムダ」。
この「7つのムダ」について、簡単な解説と要因の例、事務系に置き換えた考え方を紹介します。
この記事でわかること
・業務効率化の概念「7つのムダ」
・「7つのムダ」要因の例、事務系での考え方
・ムダを改善するための考え方
「7つのムダ」は、製造業だけでなく事務系の仕事にも応用できる概念です。
会社にも個人にも有益な業務効率化の方法「7つのムダ」を知り、活かしてみましょう!
トヨタ生産方式「7つのムダ」とは
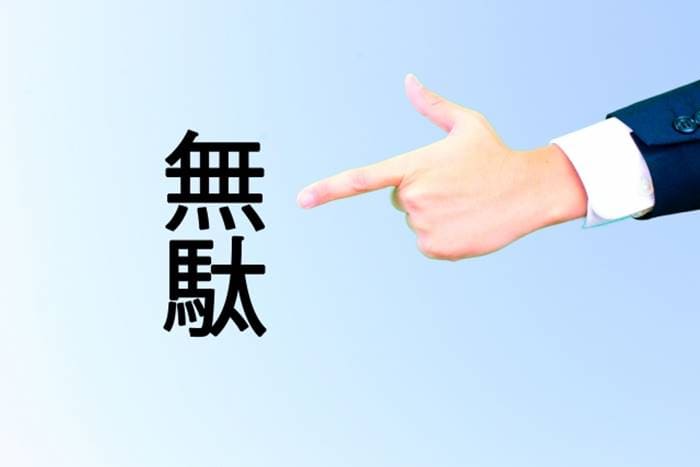
トヨタ生産方式「7つのムダ」とは、トヨタ自動車が生み出した工場の生産方式の一つ。
多くの企業が取り入れている方式で、製造業やそれに関わる管理、間接業務でも活用されています。
「7つのムダ」はトヨタ生産方式の中でも生産性向上に大きく関わる概念です。
トヨタ生産方式「7つのムダ」
・加工そのもののムダ
・在庫のムダ
・作りすぎのムダ
・手待ちのムダ
・動作のムダ
・運搬のムダ
・不良をつくるムダ
この「7つのムダ」(トヨタ生産方式)を取り入れている工場は、必要のない作業や管理業務、仕事量のムラといった「業務のムダ」を減らす意識も強いと思って良いでしょう。
加工や運搬などにムダがない作業は、作業者の負担も減らします。
そういった観点から見ても、労働環境的にある程度の信頼ができる企業ともいえるでしょう。
製造業や工場の仕事に興味がある方は、参考記事で紹介していますのでそちらをご参照ください。
-
-
参考製造業・工場勤務ってきつい?実体験から「あるある」を紹介!
この記事では、工場勤務の仕事内容や年代別の工場勤務「あるある」について、実体験をもとに紹介します。 長く続く不景気の中、求人の増加が続く製造業。 とくに工場勤務の求人関係は、有効求人倍率2倍を超えるも ...
続きを見る
基本的には工場での生産改善に取り入れられる「7つのムダ」ですが、事務系の仕事でも同じような考え方ができます。
「7つのムダ」覚え方
「7つのムダ」の覚え方は様々です。
その中でもわりと有名で覚えやすいのは「かざってとうふ」(飾って豆腐)
「7つのムダ」それぞれの頭文字を取って
「加・在・作・手・動・運・不」→「か・ざ・つ・て・ど(と)・う・ふ」
これをつなげて「飾って豆腐(かざつてどうふ)」です。
特に順番は決まっていないので他の覚え方をする人もいますが、それも同様に頭文字で覚える人が多いです。
ちなみに自分は「つてうかざいどうふ」で覚えました。
ムダの大きさ順でいくと、この順番になります。
製造業と事務系の「7つのムダ」
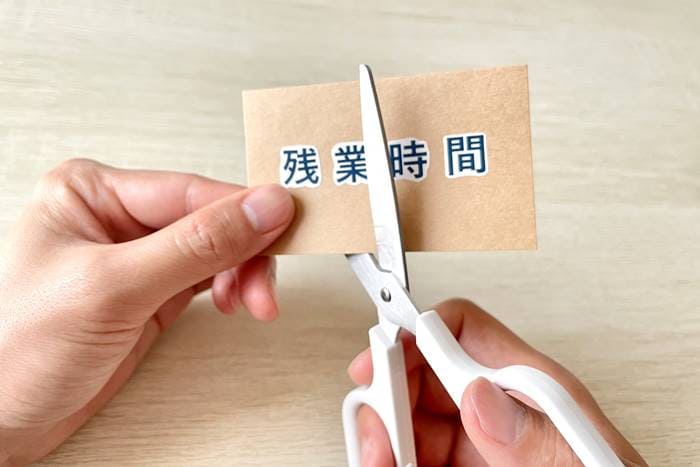
「7つのムダ」は事務系の業務効率化にも応用できます。
7つある「ムダ」を、製造業と事務系、それぞれの考え方で紹介します。
事務系といっても一般事務もあれば医療事務、営業事務、経理事務など違いがありますが、「7つのムダ」はムダの概念なのでどれにも応用できます。
加工そのもののムダ
必要のない加工作業や仕上げ作業、検査作業のこと。
どんな製品でも規格があります。
規格に収まっていれば問題ないのに、必要以上に加工するのはムダですよね。
検査作業においても、合格品を「不安だから」と再検査するなど、ムダな作業といえます。
要因の例
・見栄えを良くするために作業標準にない仕上げ作業(加工)をする。
・個人的判断で良かれと思い、規格内で追加作業(加工)をしている。
・合格品の欠点見逃しが不安で何度も検査している。
など。
・事務系での「加工そのもののムダ」→「作業のムダ」
データや資料を何度も見直す、不必要に資料の見栄えをよくする、など。
わかりやすい例だと、データのフォントや色合い、デザインにこだわったり、プレゼン資料に派手なアニメーションやオーディオ効果を加えたり。
指示があって必要であるなら話は違いますが、「この方が見やすいだろう」とか「このほうがインパクトあるだろう」といったような、個人的な価値観で作業を増やしている可能性があります。
肝心なのは「目的(指示)に必要なもの」なので、目的は何なのかをよく考えてみましょう。
社内の打ち合わせや報告会議の資料など、見た目にこだわっても意味はありませんよね。
在庫のムダ
材料や製品、全てにおいて目的や理由なく(必要なく)置かれているもの。
計画的に必要な在庫以外は、運搬や整理、管理のムダにつながります。
内示(注文確定前の未確定情報)の取り消しや顧客により製品の仕様変更などが生じた場合、処置が決まるまで長期保管になり、その管理業務も必要になります。
最悪の場合は製品の保証期限切れで廃棄することになり、損失になります。
特に作りすぎのムダが大きく影響します。
要因の例
・安心在庫など、不安からくる在庫計画。
・生産計画の精度が低い。
・在庫数管理ができていない(不正確)
など。
・事務系での「在庫のムダ」→「予測準備のムダ」
こういうデータや資料が必要になるだろう、といった確認をしない予測での準備が該当すると思います。
事務なので当然、在庫というものは存在しません。
「在庫→作り置き」と考えると、指示や確認なく「作っておく」のは不要になる可能性も高いです。
そもそも指示を受けていないのだから、作ってなくても問題ありません。
準備や前倒しが必要かどうか、確認してから作業しましょう。
いらないものを準備するのは時間のムダです。
作りすぎのムダ
必要のない分まで作ってしまうこと。
その他のムダにつながる最大のムダともいわれています。
在庫のムダ、加工のムダ、運搬のムダなど、たくさんのムダを生みます。
逆をいえば、要因を考えてこのムダを改善できれば大きな業務効率化ができます。
要因の例
・受注や在庫の管理が甘いため、余計に作っている。
・作業に手待ちがあるので作っておく。
・不良品などが不安なので多めに作る。
など。
・事務系での「作りすぎのムダ」
事務系では「必要のないデータや資料の作成」が該当するでしょう。
例えば、名前と電話番号のデータが必要な名簿に住所まで調べて追記したり、プレゼン資料に必要ないデータのページを作成したり、など。
指示されていなく、暗黙のものと勘違いして必要ない作業を自分で増やしているかもしれません。
在庫のムダ(予測準備のムダ)とも似ていますね。
そう考えるとやはり「確認」が業務効率化のポイントかもしれません。
手待ちのムダ
作業者が手が止まっている、待っている状態のこと。
時間があって、何もしていないのだから当然のムダですよね。
色んな要因でこの「手待ち」は発生します。
この何もしていない時間をどう活用するか、付加価値を生むことが効率化の鍵でしょう。
要因の例
・機械や設備が稼働中で動作完了を待っている。
・前工程の作業が終わるのを待っている。
・生産量が少なくて時間を持て余している。
など。
・事務系での「手待ちのムダ」
次の指示待ちや仕事量のバラつきが該当すると思います。
これは基本的に製造業とも同じですね。
個人的な視点で考えたら、手待ちがあるような業務であれば「忙しい」ということはないはずです。
バラつきがあるのであれば、他の担当者と分業や分散による業務の平準化がポイントになるかもしれません。
ただ、他の担当者も絡んでくると人間関係も重要になってきます。
人間関係については参考記事を上げていますので、興味ある方はこちらのリンクからどうぞ。
-
-
参考社内、職場の人間関係。「262の法則」でストレスを低減!
社内や職場、学校などで問題になる人間関係。 人間関係が上手くいっていないと、悩みやストレスが溜まりますよね。 ある転職サイトが行った「転職理由の本音」アンケートによると「人間関係が悪かった」が転職理由 ...
続きを見る
動作のムダ
作業する上で生産に必要のない動作のこと。
しゃがんだり、持ち替えたり、調べる、探すなど、標準作業にない付加価値を生まない動作です。
設備に部品をセットするときに毎回、標準作業書を確認してたらその都度作業が止まりますよね。
その分だけ作業が遅れます。
必要な道具を仮置きしてどこにやったか忘れてしまうなど、現場環境や作業教育ができていないと、こういった動作のムダがありがちです。
要因の例
・作業者の教育、訓練ができていない。
・物の置き場が決まっていない。
・作業標準で明確になっていない。
など。
・事務系での「動作のムダ」
書類が整頓されていない、PCのショートカットを使えていない、などに当たると思います。
必要な書類が整頓されていなかったり、置き場が決まっていないと探す手間がかかります。「動作のムダ」ですね。
PCの操作、特にExcelやWordだとショートカットをいくつか覚えておくと、1回の動作にそれほど違いはありませんが、積み重なると大きな効果になります。
全て覚えるのは難しいので、自分が普段やっている操作のショートカットを探して覚えるだけでも業務効率は変わってくると思います。
事務系の業務で一番手を付けやすい業務効率化かもしれません。
MOS(Microsoft Office Specialist)認定資格の勉強で一般的な操作のショートカットは覚えられるので、業務効率化のためと考えてもオススメの認定資格です。
-
-
参考MOS資格。すぐできる独学の勉強方法、必要な勉強時間を解説!
この記事では「MOS資格に合格するために、すぐできる独学の勉強方法、必要な勉強時間」を解説します。 一般的なパソコン操作スキルを証明する資格、MOS(Microsoft Office Speciali ...
続きを見る
運搬のムダ
必要のない運搬、移動のこと。
整理(いる物といらない物を分ける)も作りすぎムダがあれば、いらない物の運搬につながります。
遠回りや2度手間など、運搬で必要以上に時間がかかっていたりもします。
製造業ではよくありがちですが、同じ作業を繰り返していると慣れてしまい、そういったムダを見失いがちです。
運搬の動線を見直したり、現場のレイアウトや運搬方法を変えるなど、ちょっとしたことで改善できるムダです。
要因の例
・台車が小さく2回に分けて運搬している。
・現場に置き場がなく(レイアウトが悪く)別の場所に仮置きしている。
・必要以上に物があるため、その運搬も増えている。
など。
・事務系での「運搬のムダ」→「移動のムダ」
場所や人の移動が該当するでしょう。
製品や材料の運搬といったことは事務系にはないですが、人の移動はあります。
昨今、リモートワーク化が進んできてこのムダは効率化傾向にあるように、会社への「移動」がムダにあたるでしょう。
あとは打ち合わせや会議も、出来ればオンラインでの実施を提案するのも良いかもしれません。
残すは事務所のレイアウトくらいだと思いますが、基本的に事務系であれば職場内での移動は少ないと思います。
会社やチームで決めることなので、個人的にはあまり改善の余地がないムダかもしれません。
不良をつくるムダ
不良品を廃棄したり、修正、作り直しをすること。
そもそも、売り物にならないものに時間や材料を費やしていること自体がムダですよね。
全てがムダになるといっても過言ではないムダです。
このムダに関しては業務効率化という視点より、品質管理・改善の意識が重要です。
要因の例
・作業標準が守られていない。
・作業標準が明確になっていない。
・設備や環境の点検、確認不足。
など。
・事務系での「不良のムダ」→「間違えのムダ」
間違えることによる修正、やり直しのムダですね。
こればっかりは人なので、どうしても発生はしてしまいます。
そうなると「減らす」ですね。
こまめにバックアップを保存しながら途中経過を確認してもらうなど、修正に時間がかからない施策を考えましょう。
確認に適したツールを探すのもアリですね。
ムダに対する考え方「N・H・K・K」
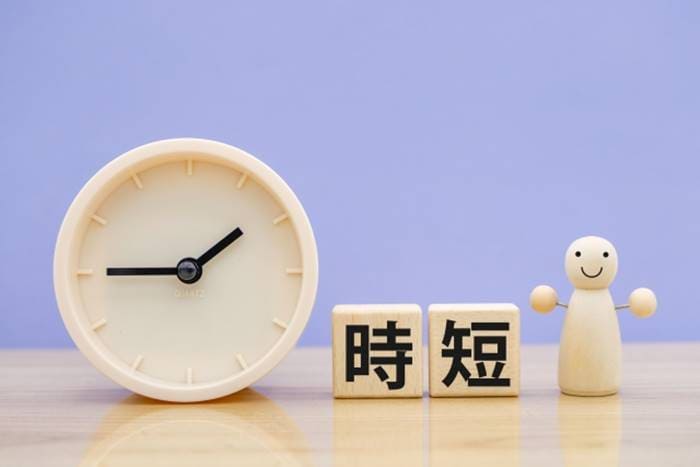
「7つのムダ」がわかったところで、どうすれば良いのか。改善できなければ意味がないですよね。
改善する考え方として「N・H・K・K」というものがあります。
これは、ムダを「無くす・減らす・兼ねる・変える」といった言葉の頭文字で、左から順に考えていきます。
ムダを「無くせる」のが一番効果が大きいのは当然ですが、そう簡単にはいかないでしょう。
無くせないのであれば、次に「減らす」方法を考えます。
減らすのも無理であれば、別の作業を「兼ねる」方法を考えます。一石二鳥という手です。
ここまで考えても何も手が打てないようなら「変える」を考えましょう。
それぞれのムダ(要因)を上げて、N・H・K・Kを基に改善方法を考え、業務の効率化を図りましょう。
まとめ
「7つのムダ」を改善することによる生産性向上、作業効率化。
なんだか当たり前のようなムダに見えますが、意外とそのムダをやってたりします。
工場ではもっと細かく、
・現場でのムダ探しや作業の定量化
・時間を細かく書いた標準作業の組み合わせ票作成
・改善の金額効果を確認
など、本格的にやっている企業も多いです。
「7つムダ」という概念は、事務系の個人的な業務でも効率化に応用できる考え方です。
自分の仕事を効率化して誰にも文句をいわれずに仕事を終え、自分の時間を満喫する。
時間を作るために転職する手もありだと思いますが、まずは手軽に挑戦できる「業務の効率化」からやってみてはどうでしょうか。
以上です。
最後までお読みいただき、ありがとうございました。